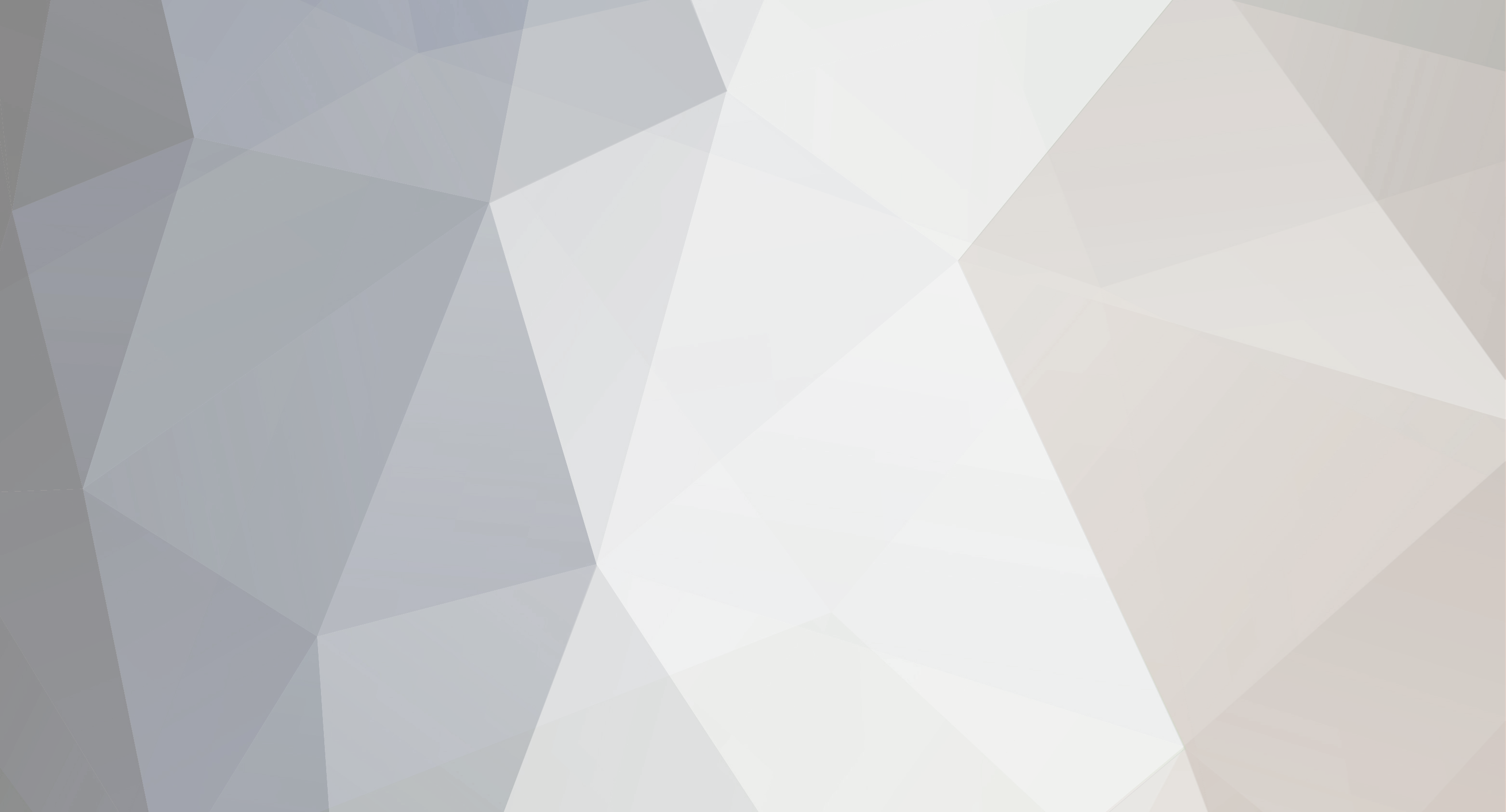
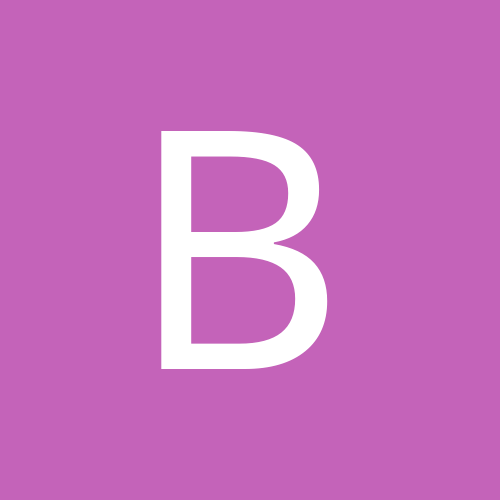
BOBEL
Members-
Content Count
82 -
Joined
-
Last visited
-
Days Won
13
Content Type
Profiles
Forums
Calendar
Store
Everything posted by BOBEL
-
So it was time to address the noise issue ahead of any more trackdays. I wanted to go with something that would work in Mondello@106db, but also be able to work on stricter tracks too. The solution I went with is a large repackable rear silencer, with a V-band on the exit for installing a removable secondary barrel silencer So with the new exhaust fitted the rear bumper valance was looking a little odd with no center exit tailpipes, I toyed with a few ideas but in the end I decided it was probably just easiest to block up the hole and mount a rain light in it. While I was at it I decided to repair the damage caused by the heat of the old exhaust. I got as far as repairing the damage and mocking up the rain light but will have to send it off for painting before refitting to the car
-
Hi Dom Yes it’s the IRP V3, it took a little getting used to on the first day. The base plate also slid forward mid session on my first outing as the mounting plate has slotted holes, and you really need to tighten the sucker down, and yet there was no mounting bolts supplied in the kit which I thought strange, luckily I had some suitable ones to hand. All in though I think it’s good but I couldn’t see myself putting it on a street car if I’m honest. Regarding temps, I’m not pushing the car particularly hard in that video and yet oil temps are high, you can see the flashing light on the AIM dash. I may have to look at more ducting as I would like to keep temps as low as possible as they have a significant impact on oil pressures.
-
It’s been a little while since I updated this thread, but I have completed the last few modifications and got two trackdays under its belt The first trackday was just to get the engine broken in, while all went well I did however notice that oil temps were rising quite rapidly, and I typically don’t like to see over 110 Deg C. Prior to the power hike and engine build oil temps were easily kept in check with the HKS oil cooler but after the first outing I reckoned more air needed to be directed to the cooler. Best option was to remove the lower bumper lights and replace with mesh, I opted to do both sides just to keep the symmetry Last little addition was an AIM smarty-cam to connect up to the dash, I’ve messed with GoPros for a while but always find it fiddly and more often than not I forget to turn it on or its battery runs out, whereas this logs constantly and the instant data overlays is very handy Some footage from the first try, I have some fiddling to do with the track map settings but otherwise it was very easy to use and setup. Best to disregard some of the lines in the video above, I’m still recalibrating with the increase in power and lack of track-time recently but it certainly has the makings of a fast car, also a new set of tyres are required After the first two track-days there are two items on the list to address I seem to have developed what can be heard in the video as an issue on 3rd to 2nd downshifts, which I reckon is synchro related, I’ll have to look into it at some stage but I’ll give it another day or two before pulling the gearbox again. Second and more pressing issue is noise, I’m currently too loud for track easily over 106db so it will be off shortly to get a new repack-able rear section, and a bolt on secondary silencer that I can attach trackside if need for some of the even more stringent tracks like Oulton etc.
-
I’m not entirely surprised by the results to be honest. The pressure drop across an oil cooler is 10-15psi temp dependant and it looks like that have just bypassed the oil cooler and gone into the mains using a very large oil filter. It’s an interesting solution and something I might look at myself but I do wonder what impact it has on oil temperatures on track. It would be an interesting experiment, if it has a detrimental impact on oil temps that would suggest significant flow is required at the mains gallery and would concern me even more.
-
Did a few calculations based on the revised gear ratios with the PAR gear set. To see how it fits with the torque curve. Should see me stay in the meaty region in all but the 1-2 shift.
-
So the car made it onto the dyno yesterday for tuning 😀 Pretty pleased with the results, made just over 11psi, and the torque curve holds nicely from just beyond 4,500 rpm up to 6250 rpm which is mapped really nicely for a centrifugal charger IMHO. Peak power comes in around 6250 - 6750 rpm so means I won't have to chase the redline to get the best out of it on track and hopefully will keep me in the range of good oil pressures too.
-
So finally over the weekend I got the new engine to fire up. When I initially tried to start the engine on its base map I just couldn’t get it to start. I checked over everything and got my tuner logged on remotely and we began to trouble-shoot. I initially thought maybe the new fuel pump was acting up but the newly installed pressure sensor was showing good pressure (paying for itself already!) The issue was manifesting as stall on cranking which we thought was maybe a lack of cranking amps from the battery, which to be fair we had stressed while trying to trouble shoot. I really couldn’t understand where the issue was coming from but I had my suspicion that the battery was probably not the issue. Then by chance while researching the issue on-line I came across this article and it all started to sound too familiar. https://www.picoauto.com/library/cas...gine-non-start Just to be sure I dug out some photos I’d taken during assembly and sure enough I could tell I had made the same mistake when setting the timing. And it appears I’m not the first to have done it either. Having gone through the OEM manual again I can see exactly how I made the mistake, luckily when you do make this mistake you essentially set the right bank 180Deg out of phase so there is no valve interference but it does mean the front cover has to come off. In the end I opted to strip the front off the car and do it in situ. Once the timing was sorted the engine fired up first turn of the key. I haven’t run it up to temperature yet as it will be broken in on the dyno, so I can’t tell how many oil leaks I have yet....but fingers crossed! Once that was completed I spent a bit of time configuring the CANBUS signals between the Motec ECU and AIM dash. Currently I have the oil pressure sensor routed directly to the AIM dash to control the Accumsump but I plan to re-wire it via the Motec to utilise the inbuilt rev cut, then relay the signal over CANBUS to the AIM dash. As the AIM Dash is receiving two CANBUS signals (ECU, and OEM Chassis CAN) but it can only run its inbuilt template on one channel I’ve had to remap the OEM chassis signals on the second channel. It’s quiet simple to do once you know the addresses etc. The info might be useful to other 86 owners so the signals I’ve mapped are below. I’ve only mapped these few as they are the main ones I’m after. So that’s it for now, my final part still hasn’t arrived yet but as soon as lockdown is lifted it will be off for dyno tuning.
-
Interesting solution, great to see people coming up with different solutions, and it appears it would be easy enough to implement too.
-
On the oil temp sensor I just left it in the stock location, I toyed with the idea of shiming it back out a little bit in the end I just left it as is for the moment.
-
Hi Mate On the Accusump I went with the Canton recommendation which was a 2qt unit, from what I can tell Fensport actually run the bigger 3qt but I wanted to install it in the battery location and in combination with my baffled larger sump I think I’ll be OK. I’m not aware of a specific race version to be honest, the variations seem to be the valve that you use, they recommend a manual valve or the electronic valve with pressure switch for race cars, which is what I’ve gone with but obviously I’ve deviated from that somewhat by adding sensors and having the AIM MXP control it. Thanks for the heads up on the fuel pump and starvation issue too, I see Fensport have the door flap on their site so I might pick that up at some stage and fit it too. I run on both slicks and R888 so I’ll probably see similar.
-
Thanks for looking that up for me, really appreciate it. In the mean time I’ve actually discovered the true cause of my problem, unfortunately it’s a little more complicated than a new battery!
-
Thanks for the reply Nice numbers, I will probably end up going turbo at some point myself. Ye same battery I’ve run up to this point, same location etc, I wasn’t keeping an eye on revs to closely at the start as we troubleshot a few things but tuners log said they dropped periodically, I’ll juice up the battery and try again just interested to know if maybe my CCA is low for a 12:1 built motor.
-
Interesting power figures, to be honest I’ll be happy enough if I get near those for now. What power are you making with the HKS turbo? Also another somewhat related question given your built engine and supercharger experience, did you find the engine hard to crank? Myself and my tuner failed to get the engine to start yesterday and it appears my current battery Odyssey Extreme 30 with 400cca might not be up to the job, just interested in your experience?
-
Are these sold?
-
Not a huge amount of progress lately, to be fair there isn’t a huge amount left to do aside from some little jobs. First one was to find a home for the USB/Comms ports for both the Motec and AIM Dash. There was just enough room in the centre console below the battery kill switches so I installed them there, plus it makes them very easy to access, although in truth I could have hidden the AIM dash port as it has built-in WIFI so I probably won’t need it that often. Also finally installed the dash with all the wiring now finally completed behind it. On the back of a little more research and talking to Tuner who’ll be mapping the car I decided it was probably best to add a fuel pressure sensor so I cut into the line just before the fuel rail and added a 150psi sensor. Handily the Motec has a 12 Pin Deutsch DTM breakout plug as part of the GT86 patch loom that is pinned out to accept the fuel pressure sensor, I put a 3pin DTM just the far side of the firewall as I’ve done with all the additional sensors just to aid quick removal, and then ran back to the passenger footwell where the breakout plug is located Last little wiring job was to fit a new 3Bar MAP sensor, as the OEM will be easily maxed out with the unrestricted Supercharger at the upper end. Once that lot was done it was down to the more mundane. First was filling the coolant system. I use a vacuum system for this as it gives the most reliable method of ensuring there is no air in the system. A quick little test showed the system was holding vaccum so in went the coolant. Final job was to prime the oil system. For the moment I want to leave the Accusump disconnected until I have the engine run in, I just don’t want the initial break-in oil going into the system In order to fully prime the engines oil pump and all the oil galleries I filled up the front housing ports via the oil filter housing, and then connected a 1.5L oil syringe to the top of the main oil gallery and forced about 1Ltr of oil through the system. I’ll do the same again immediately prior to first fire up too. So that’s about as far as I can go now until the engine is started up. There is a bit of a delay with my tuner at the moment for obvious reasons but I’m also just waiting on delivery of one final piece which I’m hopeful it will arrive in the next few weeks.
-
Hi I’m actually running a Fujitsubo / Gilken Centre Exit rear section, only the mid/front pipe is HKS, you can kind of see it in the photo below. I can say that even with the OEM second cat in place I was right on the noise limit at Oulton, so if you intend on doing a lot of trackdays beware of the exhaust you choose. I may need to do something myself now to keep it quiet.
-
Thank you [mention]Lauren [/mention] Yes a few of us travel over every now and again for Trackdays, mostly Anglesey as it’s so close, but we’ve done Oulton park aswell. I’ve previously done Time-attack, not in this car mind you, the GT86 has only been a trackday toy up to this point, unfortunately there is no longer a time-attack championship in Ireland and I don’t want to do wheel to wheel as the car is just too nice for rubbing. I’ll caveat all of the above by saying regardless it wouldn’t show the potential of the car as the biggest component that needs replacement is ME [emoji3][emoji3][emoji3]
-
While I was waiting on the paint on the catch can bracket to dry I set about finally fitting the finished Accusump bracket complete with the wiring etc.Once fitted I went back to the catch can... I have a bit of a thing for keeping as much as I can in satin black just so the engine bay doesn’t look like a complete mess.Next up was to bypassing of the heater matrix, I just looped out the supply and return line using the high point bleed so that I can still properly remove air from the system. I also blanked the port on top of the intake manifold, where the vacuum line originally ran to the PCV, and the two lines back to the heater matrix.After that was sorted I fitted the new -10AN line running from the accusump to the oil gallery plug, I also fitted the oil pressure sensor that runs back to the AIM Dash for logging engine oil pressure and deployment of the accusump.While in that area I also blanked off the HKS intake port that the front crank case vent previously ran too.With that completed I set about fitting of the new bosch wideband lambdaI wasn’t sure where exactly to mount the Motec Lambda to CAN module, I left the CAN lead I ran from the ECU long enough to give me a bit of flexibility, and I finally decided to put it on the back of fusebox lid, it’ll keep it well out of the way and shouldn’t be too hot there either.Last little job for now was to fit the DW fuel pump. You can see that it’s a little bigger than stock but it fits in the OEM holder with a little modification of some retaining clips.
-
Managed to make some progress over the last few days, thankfully the Radiator, shroud, and exhaust parts arrived even sooner than I was expecting so I got stuck in....First was to take out the OEM radiator and shroud and fit the Mishimoto rad, you can see just how slim the OEM one isI was a little concerned that with the shroud attached the new setup would be too wide and might foul the HKS supercharger intake pipe that sits behind it.Luckily it just cleared the pipe with a few mil to spare so it should be fine.Next on the list was the exhaust manifold, I won’t make the mistake I made with the original and if I happen to take it off the car for any length of time again I’ll fit the spreader bar that comes on it when shipped.With it wrapped I fitted to the car along with the new HKS MidpipeWith that lot out of the way I switched my attention to fitting a catch can. I haven’t run one up to now, but I did notice some residue in the intake manifold when removing the original engine, plus with a build engine running more boost it’s not going to get any better! Space was limited and I wanted to run a vent to atmosphere system with both the PCV removed and also run the front Crank case ventilation line to it too.I finally decided on using the space left on front of the passenger side strut tower.First up I popped in some rivet nuts to mount a bracket and then I cut out a simple aluminium bracket to mount the can too.
-
So that's pretty much the status of my build at the moment, hopefully the remaining parts will arrive shortly and not be delayed to badly with all the recent restriction. I'll update as I go from here on 😀, no more historic copy pasting....
-
More recently progress have been slow and unfortunately the 86 has started to fight back... First up was the install of the new straight cut gearbox, I must have spent 8 hrs under the car trying to align it. The pilot bearing alignment is a real pain on these cars and as it turned out my improvised alignment tool which has worked previously didn’t like the combination of a slightly worn clutch plate. So I had to wait a week for the specific Subaru alignment tool to arrive, and luckily it did the job and within an hour the gearbox was fitted. (Lesson learned on just buying the right tool for the job!) Next was a fight with the exhaust manifold, after taking it off the car it lay on the floor for about 2 months. However when I went to install it onto the new engine it just wouldn’t fit, nor would it fit the old engine, so clearly it had deformed while sitting off the car, presumably from heat cycling and residual stress. I tried spreading the flange plates with a bottle jack but it just won’t hold a shape and keeps springing back regardless of how much pressure I put it under. So unfortunately I’ve had to purchase a new manifold which I’m waiting on. While at it I’ve decided to take the plunge and change out the only remaining piece of OEM exhaust which was the front pipe with contains a secondary CAT, so I’m going replace it with a new twin resonated HKS front pipe. The final punch was the coolant system, and I have to take responsibility for this one, about 3 yrs ago I noticed the car was low on coolant while on track. At the time I kindly got some coolant off a Friend to keep me going. I gambled that it would probably be OK, but I wasn’t aware just how unique the coolant was in the GT86 and that it would react so badly with the topup. Unfortunately while taking apart the existing coolant system I’ve noticed that it is full of red silt and it’s pretty well much stuck to every surface. By comparison the donor cars coolant system was squeaky clean after 20k miles As the car sits now I’ve installed the donor cars radiator and piping, and reinstalled the supercharger However having thought on it some more I was not happy that the heater matrix will still be a source of silt and I can’t flush it out sufficiently so I’m going to bypass it. As this will put a little more pressure on the coolant system I’ve decided to upgrade the radiator to a high capacity Mishimoto Radiator and add their upgraded shroud with larger fans, to be fair the OEM radiator is very thin....so the front end will be coming off again once they arrive, assuming COVID doesn't get them first!!!!! Thanks again to Part-Box for the latest round of purchases too [mention=2716]Lucas@PartBox[/mention]
-
Eventually I got around to lifting the original engine out of the car and sitting beside the new short block Unfortunately the progress after this was not a swift as I hoped. I ran into quite a bit of difficulty trying to get the valve clearances correct. Toyota love me, this is the First round of shims I bought off them!! Essentially I built up the engine with the first set of shims installed, all clearances were within spec, and I got as far as setting the timing. At this point I rotated the engine by hand and rechecked the clearances only to find they were out of spec, some by a significant margin. I came to the conclusion that the valves with the new springs installed had seated properly when they were rotated through a full rotation of the cams. So hence back to Toyota for round 2 and another lot of shims! A further 10 shims later, at 13 Euro each and suffice to say the heads had worked out quiet expensive. It took a few weeks to get beyond the valve issue, and it was a real pain to have the engine assembled only to have to take it apart again, but at least now I can claim I’ve built the engine twice!! I also got another attack of the “While your in there” and bought theses DW 900cc Injectors (Thanks to [mention=2716]Lucas@PartBox[/mention] and a DW 65c (265 lph) pump which should keep the injector duty cycle sensible and ensure the fuel pressure doesn’t drop off at the top end. As the engine is 12:1 comp ratio and will be running unrestricted it may take a little enriching to keep knock in check.
-
While at it I also disassembled the oil pressure relief valve to inspect it and make sure there was no debris from the porting that had been done on the oil galleries in the front cover. As I couldn't really progress any further with the engine build until the new shims arrived I turned my attention back to the car and its current engine and gearbox. Safe to say I’m covered from gearboxes anyway. Although I’m really hoping the PAR straight cut gear set in the second gearbox in the photo below will mean I don’t need the backups any time soon!! Next up was to take the HKS supercharger off the existing engine, as I didn’t want to drain down the cooler, filter etc as the HKS oil is just stupid money and I’m not near needing an oil change, I opted to take the entire front off the car and managed to remove almost all the setup intact without breaking any lines. To be fair removing the engine and installing the new one is much easier with the front off anyway. While at it I removed the restrictor plate that the supercharger is currently running with, and you can see from the grime how much larger the intake will now be! With all that removed the existing engine was ready to be lifted out. I also needed to swap over a few bits and pieces that were modified to fit the supercharger originally so I planned to do that while all engines are out on stands.
-
The Short block eventually has landed back from the machine shop with the shiny new rods and pistons installed.First up was to build up the heads which have been skimmed and lightly ported, The valve seats were also cleaned and valve shoulders re-cut so I was concerned that valve clearance may not be correct even though any changes were accounted for by adjusting the valve stem length.Unfortunately with the heads reassembled and clearances checked multiple times, there were quite a few out of tolerance.I want to have all the valves clearances not just in spec but sitting at exactly the same clearance, so I’m currently waiting on Toyota to get the exact shim sizes into stock. It held me me up a little on building up the heads but I wanted them perfect.There is also a know issue with valve seat compression where the valve clearance on some newer low mileage cars actually go out of spec (tighten) and cause major issues and perhaps that was the case with this engine.Another issue I came across was that one of the oil control valves in the heads was actually damaged, they are essentially a small strainer that restricts oil flow into the heads. I’m not sure how it happened perhaps during my cleaning, but regardless I’ve replaced all four of them in the two heads.While waiting for the shims to complete the heads, I cracked on with the other end of the engine, fitting the lower cradle and new larger diameter pickup tube. Aside for that I spent an awful lot of time cleaning and degreasing parts and wire brushing bolts to clean the threads for reinstall! You really don’t see much progress for a full Saturdays works.As the heads are made up of three parts I was able to go ahead and torque up the mains with the ARP studs and nuts, and new thicker Cosworth head gaskets.The ARPs are torqued up to 95Ft.lbs each and it feels a little sketchy as it’s so much force but they all got there in the end.
-
The last few weekends have been spent wiring up and figuring out the best locations for all the various bits and pieces needed for the accusump, AIM MXP dash and the Motec ECUI’m was not a fan of the Binder connections that came standard on the AIM looms, their an absolute pain to wire/solder so I converted any connections I’m using to Deutsch DTM, and likewise any wiring running to the engine bay has DTMs on that side of the bulkhead so that everything can be easily disconnected.I’ve also made sure that the accusump wiring allows easy removal of the relays and fuses within the engine bay and I picked up a 12” extension for the schrader valve so that it can be routed to a spot that will make topping up the air side of accumsump a doddle in the engine bay.The way I’ve wired it only requires one relay to be pulled and a small bridge installed to default the full setup back to the basic pressure switch setup. If the need arises it will be a 2 min job trackside.Next up was finding a home for the Motec M150. Unfortunately because the roll cage footing sits where the standard ECU would normal be mounted in the passenger foot-well it was not possible to fit the Motec there, in fact the OEM ecu has always just been hanging freely off the loom so not ideal regardless.I decided the glove box was probably a good location for the M150 and it would keep everything nicely out of the way.In order to route the Motec loom so that it could pick up the standard ECU header I had to cut the side out of the glovebox and also make a bracket to mount the M150 on.After some fettling and a little bit of paint on the bracket it was sitting nicely in the glovebox. I also pinned out an extra CAN output from the ECU to run to the MXP dash, and while at that I created a new lead to extend the Lambda to CAN module so that it can be mounted in the engine bay where I’ll be putting a new Bosch wideband Lambda Sensor in the exhaust header.