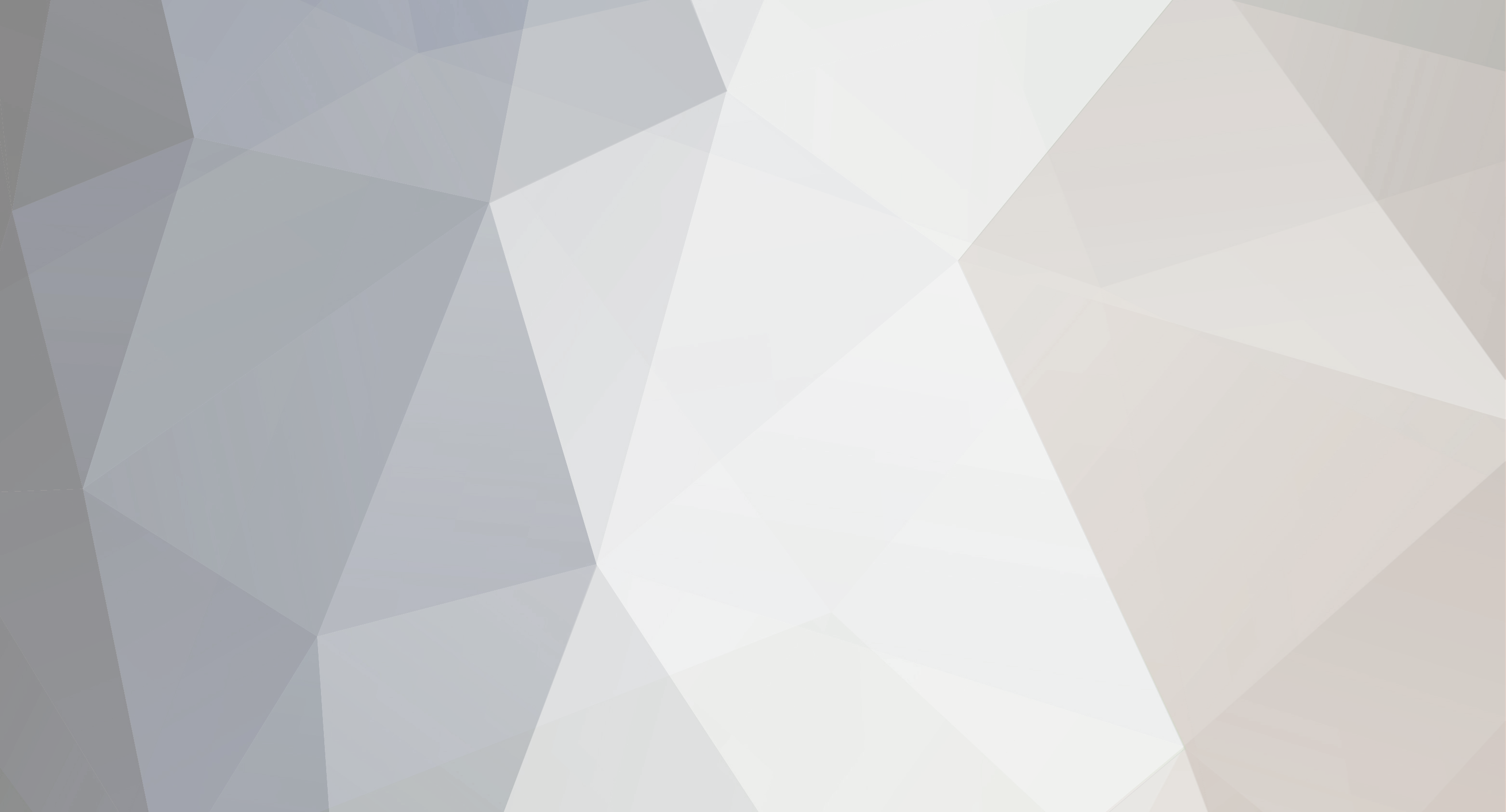
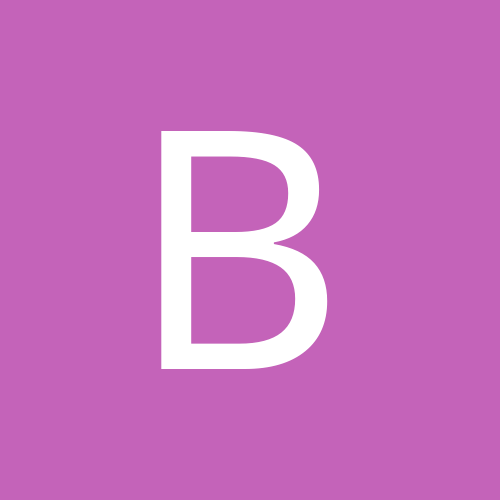
BOBEL
Members-
Content Count
82 -
Joined
-
Last visited
-
Days Won
13
Content Type
Profiles
Forums
Calendar
Store
Everything posted by BOBEL
-
To be honest I’m not 100% sure on it, I believe it’s part of the DAMD black edition aero kit that was originally installed by JRM, it’s a one piece fibreglass part that covers the entire boot lid.
-
No major skills involved, I certainly wouldn’t call myself an expert by any stretch, I’m an Engineer by profession but mainly I’ve just been a weekend worrier for a long time [emoji3]
-
Thanks, it’s been a labour of love over the last 3-4 months in particular since I started the engine build and all that’s gone with it. I have a few more posts to copy across then it’s pretty much up to date. And like all good projects its still a work in progress, so I’ll keep it to real time updates going forward.
-
I'll also apologies at this point for the onslaught of posts, as some of you can probably tell I'm copying it across from a long running build thread on a local Irish forum, but though people on here might like it too, and to be fair I've purchased a lot of items and got a lot of support from traders on here so was time to give some love back
-
Thanks dude, the thought did cross my mind 😁
-
After this I had been struggling to make any noteworthy progress for a little while, mostly fettling brackets and wiring, however then this arrived [emoji3] The MXP has some great functionality, aside from a nice display it has two CAN-BUS inputs which will come in handy as I will be logging from two different CAN-BUS sources! It allows logging at up to 1,000 hz and track mapping with GPS, so I might actually find out why I’m so slow!! However the real benefit is the ability to log all the engine data and display it. So wayward Lamda readings, Knock etc. can be setup to trigger LEDs or alarm messages, the possibilities are pretty much endless. The other major plus is that it contains two Digital Outputs which I will be using to control the accusump based on certain conditions. It’s very easy to set up and with the Digital Outputs acting as a bridge to ground for a relay it can be used easily to control anything. Below is an example of the simple logic to discharge the accusump which means it can be set to whatever pressure I want. The Plan was to mount the MXP into the centre console where the Radio unit would sit in a road car. I mocked up a little backing plate to epoxy onto the dash trim, admittedly it’s a little rough but it will be going satin black and wont been seen behind the unit. Little test fitting While I was still waiting on the engine block to come back from machining I was also looking around for someone who could map the car once back together using EcuTek as that is what the car is currently running on. I have previously got it remote tuned by Abbey Motorsport as I'm based in Ireland but given it will now be running a fully built motor I really wanted a full Dyno tune. After contacting a lot of places no-one was able to offer EcuTek tuning in Ireland or were familiar enough with it and the GT86 to make me comfortable. The only options were take the ferry across, but if I want to tweak or modify further it’s a little limiting so with far too much time on my hands I convinced myself the best option was one of these As an aftermarket ECU they really are on another level, the GT86 package is fully plug and play with custom harness, plus it fully integrates with the OEM CAN-Bus, plus it gives me the option to get it tuned here, and I’ll be able to tweak the map myself using the software. In combination with the MXP I will also be able to read the M150’s own CAN-BUS protocol giving a lot more channels then the OEM CAN-BUS too.
-
The standard Accusump set up is pretty basic, and was a little limited for my liking, It comes with a pressure switch which activates when oil pressure drops below 55 psi and closes again when it rises above 60 psi, if wired into an ignition feed it will also pre-oil the engine on startup. However I want to add a lot more intelligence to the setup and as a result I went down a serious rabbit hole! Dismantling the centre console to identified where I could tap into the CAN-bus, and how I’d get through the firewall with all the wiring, and where I would get power from!
-
After a chat with a few trusted engine builders and doing some more research I concluded I really couldn’t afford to not incorporate an accusump it my build. The fact that Mountune needs to put one on its BTCC WRX cars, and most professional BRZ/GT86 race cars seem to run them too it was too big a coincidence to ignore. Next was the challenge of fitting this sucker into the car, I wanted to keep it mounted in the engine bay and as close to the oil gallery plug leading into the main bearing oil gallery. Room is limited and all other installations I’ve seen have mounted the accusump directly above the engine sitting on top of a strut tower brace but I believe this requires some modification to the bonnets sub-frame to allow it close properly. I’m not a fan of this for a few reasons but mostly the fact that any leaks will drop straight down onto the engine or spray across the underside of the bonnet. Luckily the car has the battery relocated into the passenger’s foot well so I was left with a nice area to try and place it, I was at a loose end as I waited on the engine block to return so after hours of tweaking and modifying I finally ended up with this. It should shield any potential leaks from spraying all over the place and it will also give me some mounting locations for some other stuff I have planned! Trying to find pickup points for the bracket proved difficult but with the AN-10 hosing routed where the red line is shown it should work pretty well. The protective film will be removed and it will all be going a nice satin black and look more subtle. The final install will be completed once the new engine is in.
-
SO....I say I had planned to have the donor gearbox on hand as a spare but I think my next purchase truly pushed me well beyond the budget build philosophy! While browsing on another owners forum I came across a chance I just couldn’t pass, a freshly built straight cut gearbox complete with carbon synchros. There really aren’t many of these around. Essentially it’s a standard gearbox casing with PAR Engineer full internals, a 1 through 6 straight cut gearset, upgraded bearings, shafts and unusually it was rebuilt by PAR themselves with carbon fiber synchros as the previous owner went to the trouble of shipping it to Australia. One of the big attractions apart from the epic straight cut gear sound it makes is the fact it remains a manual and you still get the joy of rowing through them. Some stock photos of the internals, as obviously you cant see them now [emoji3]
-
After a lot of research and speaking to another owner who built his engine too I think I’ve found a solution the OEM excessive RTV issue aswell. This sealant is anaerobic and only sets in the absence of air, but will seal any machined surfaces as well or better than an RTV, so even if it’s over applied and gets near an oil gallery it simply stays in liquid form and is flushed out by the oil, causing no hard to the oil pickup or oil supply. I wasn't able to use it in every location as it requires a very small gap tolerances between the mating surfaces but it worked well for most of the long block which is where these engines give most issues! While the block is off at Westward Engineering I kept entertained by stripping the donor car of a few more bits. The standard gearbox is weak, and a lot of people have had failures in and around 400hp, while I don’t intend to run that much power my plan was always to have a spare gearbox on hand if required, and while liberating it I also pulled out the rear diff. I had planned on maybe trying a different final drive ratio, I find the OEM gear ratios don’t quite suit in a few places around my local mondello park.
-
In the end I struggled to get the exact bearings I was after, I did eventually get the polymer coated variants for the conrods but had to compromise and get the non coated version for the mains, to be fair the conrods are my main concern anyway. Viton valve stem seals also arrived The main reason things have stalled however is that I was waiting on the machine shop to complete the machining of the main block halves. I’ve also asked them to throw in the rods and pistons as-well, I had hoped to do it myself but as I didn't have all the measurement tools or ring files so it just made more sense. However while having a good chat with the shop, they did suggest that I go with a thicker head gasket than OEM to compensate for the skimming of the block and heads as I’m already at 12:1 compression and supercharged. I decided to go with 1mm thick Cosworth gaskets, which is about 0.4mm above the OEM. When I was at it I picked up a few other bits too, mostly required for reassembly, got some ACF-50 to give it a shot too, also opted for some up rated HKS plugs.
-
Also went with a new set of OEM main case bolts, they seem to be commonly used in a lot of builds so will be more than up to the job For the head bolts I’ve gone with ARP hardware. The OEM are a bolt type whereas the ARP are a stud and nut design, but again pretty much every builder seems to use them I had also been looking for some up-rated GSC viton valve stem seals and I finally found some with a supplier. But I was really struggling to get the new bearings. I wanted to go with KING racing p-max bearings and their newest polymer coating (p-kote) for both the mains and rods as it will give a little margin of safety in low oil supply situations, but a lot of suppliers were struggling to get me a set so the build ground to a halt for a little while.
-
Next on the list was a set of Pistons, the OEM ones wouldn’t fit the Carrillo rods anyway. I opted for a set of JE forged pistons. I was a little torn what route I’d go in terms of compression ratio, I thought of dropping down to 10:1 as is more common on boosted engines In the end I decided to stick with 12:1 and go with a very small +0.25mm overbore, to allow a very minor boring of the cylinders so that their fitting perfectly. I’m not chasing huge power and with sticking supercharged I think the 12:1 compression will keep low rev responsiveness in check What I like about the JE pistons is they have a nice meaty top ringland and a shorter skirt length, they also have a 22mm wrist pin, and by retaining 12:1 compression it means they also have more material above it too. Also picked up a few more mundane pieces. OEM gasket kit, surprising number of gaskets in it given the amount of RTV involved, but it includes a set of OEM head gaskets that I’ll be sticking with too.
-
After a little wait Parts finally started to arrive for the rebuild. First up is some new springs for the heads. I went for a set of GSC Beehive springs with titanium retainers. The benefit of the beehive design coupled with the retainers is they will support upto 9,000 rpm rev limit, I’m unlikely to go there given the oil system limitations but I will try and push higher than stock, Ideally 8,000 rpm New Beehive spring kit on the Left versus OEM on the right Difference is a little more obvious side on Next up was some new connecting rods. My original plan was to buy a budget set of Brian Cower rods with ARP bolts and keep the OEM pistons, but once I had the engine pulled apart it seemed nuts not to do the build I really wanted to so I bought a set of Carrillo forged H Beams rods with the upgraded 3/8” Carr Bolts. They really are the best rods for the FA20 by a margin. As you can’t crack a forged rod Carrillo overcome this by machining a saw-tooth pattern into the cap and rod. I don’t know of any other aftermarket rods for the FA20 that does this but I just love the attention to detail, even if it’s at a price.
-
With the engine torn down it was time to tackle the mountain of RTV that was on everything in sight. A combination of the three below with various types of scrapers and brushes was somewhat successful, with enough patients it would eventually take most of the RTV off a surface, and the remainder would come off with a pressure washer but it wasn’t giving the super clean finish I was after. The other issue was the casting on the engine block and front cover are very rough from the factory and suffer badly with oxidation and no amount of chemicals and pressure washing at close quarters was going to leave them looking nice So after losing the will to live, and valuing my hands and lungs I decided to send the parts off to a local guy who does Vapour blasting. A friend had used him and he was highly recommended. As it turned out he was an absolute gent and a car nut, with a lovely 911 and BMW 2002 out the back of the workshop. I have to say his attention to detail was only what you could get from a proper car guy too, he was extremely careful to protect all the bearing journals and plug all the oil galleries. Nevertheless I fully de-greased, and power washing all the parts again for good measure to ensure these is no small particles anywhere before they even go for machining where they'll get cleaned a few times again. But I think the results speak for themselves, you can still see how rough the castings are, and nothing short of polishing them would remove that but they look better than factory fresh IMHO. While at it he also de-carbonised the cylinder bowls, and each of the valves. the heads themselves will get skimmed so mating surface will be cleaned up when machined.
-
The other piece of the puzzle is the front cover, the oil pump assembly sits in the front cover and all the oil feeds to both heads, and the main block are routed through it. Its a bit of an unusual set up as the supply lines are simply covered with machined covers and held in place with machine screws, there is no sealant on the covers so they just pop off, its almost hilarious that they covered the engine in RTV yet don't seal these covers which hold back all the oil pressure, and any leaks will drop oil pressure to the engine itself!With the covers off you can see the oil pump and feed linesPlan was to port the lines that lead to the main gallery only, the heads in the FA20 don't suffer from a lack of oil flow and the main gallery is not a priority feed either so the LHS head actually gets fed before it.So it might be all well and good enlarging the galleries but it won't be much good if the pump cant keep up! So I planned a few other modifications tooFirst up a new, high capacity oil pump. The OEM pump has a strange profile, and its also sintered metal and has been known to fail in some engines, so the replacement is a billet piece with the same profile as used in the FA20DIT as found in the Subaru WRXSo the pump should look after the increased oil supply but only if it can get the oil from the sump in the first place, so to help that I'll be changing the pick up to a larger type with a straight line from the sump. The OEM one is a smaller diameter and has a restrictive bend in it too, a few people has noticed cavitation marks on the pump housings during builds so hopefully this will address this too.The other benefit is the upgraded pickup has a larger mesh too so hopefully its not as likely to clog from strands for RTV!!!
-
So with that lot apart it was time to examine the oil galleries and come up with a plan to address the FA20's shortcommingsFirst up is the crank, the crank has 5 main journals, but only 3 of them provide oil to the 4 big end journals, and here in is one of the issues, almost 100% of bearing failures in the FA20 are rod 2 or 3, and if you look at the crank you can see why.The first main journal on the right feeds Conrod 1, and the last main journal feeds Conrod 4, so that leaves main journal #3 feeding two conrods yet it isn't sized to supply twice the oil volume, so whenever oil flow/pressure drops in the engine these two rods get starved and eventually you end up with at least one of them spinning a bearing.The main galley runs just below the journals where the red arrow is show and the plan is to drill it out to 12mm from the front of the block as far as No.3In order to get the full benefit though, the galleries the whole way from the pump supply in the front cover really need to be enlarged too.So the front of the block needs to be ported where the oil enters from the front cover. The oil path to the main gallery below the journals is a bit convoluted as its not a straight shot from the front cover, it comes in the top hole, travels down and then into the block, the hole that actually sits at the front of the main gallery in the picture below is capped with a timing chain tensioner but at least it will allow access to run a 12mm bit down the main gallery.
-
So with the heads out of the way it was time to split the block, even the head gaskets get some RTV for good measure, there was a surprising build up of carbon in the cylinders too for a low mileage motor!With the gasket removed I did however noticed a lot of sludge built up in the coolant passages which is a little concerning, I've heard of others coming across this aswell, apparently some form of coolant contamination from the factory sealants or something, but it had me contemplating a switch to running it on a waterless coolant.Next up was splitting of the block, and as expected they decided to glue the bloody think together aswell! To be fair prying most of the sub-assemblies apart was relatively easy with the right tools and a bit of care, but splitting the block was a bit of a pain, you can see the seams of RTV running down where the block halves meet.A few taps of a rubber mallet was never going to do the trick so I broke out a mini bottle jack and gently pried the halves apart at the bell housing end, while being careful not to damage the block, eventually the two were apart
-
The RTV party continued at every turn....I've heard of places billing huge hours just to clean an FA20 down for reassembly, I can understand why!The heads have a couple of caps etc but they also are made up of two assemblies, the cams sit in a cradle assembly that sits above the heads themselves, again plenty of RTV for good measureWith the cradle and cams removed I could finally get access to the head studs to take off the heads.At this point the sensible thing to do would have been leave the heads alone, just stick with the original plan to drop in some relatively cheap rods, a good set of bearings, keep the OEM pistons and call it a day.....so obviously I didn't do that... so out came the valves, and springs
-
With the engine loom stripped off it was time to whip off the front cover The timing chain assembly was whipped off, there is a certain technique needed to move the cams and crank to certain rotations so you don't end up with valves meeting pistons as you take the second chain assembly off Once the timing gear was out of the way it was time to dissemble the long block, as the FA20 has a lot of subassemblies it takes a while to fully strip down First up was the heads, relatively easy but shows the first signs of the major issue with RTV sealant....its bloody everywhere, under seals, on every mating surface.
-
So with the engine out, I started to strip the block. First up was to strip off the inlet manifold and remove the fueling systems, the beauty of boxer engines it you have two of everything, two high pressure fuel rails for the DI system and two low pressure rails for the port injection etc etc.... Finally with some of that lot removed the main wiring loom is exposed so that it could be removed.
-
So the GT86 has been happily soaking up the trackdays for over 2 years, it wanted for nothing more than regular maintenance and consumables, but I'd been fighting the urge to tinker with it for a while. The car has been running with the HKS supercharger on a stock engine and while it shows no signs of being unhappy its only a matter of time with the FA20 engine before a bearing spins or the connecting rods decide they want to leave the party. My plan was to address the weakness with a simple build......the purchase of a second GT86 as a parts car really should have been a clue that my "simple" build philosophy was doomed! So first thing up was to liberate the FA20 engine from the parts car, a relatively low mileage 2013 GT86 that had a fondness for ditches! So after relatively little effort the little boxer engine was happily sitting on its stand! At this point I was still in denial that a sensible simple build was still on the cards!
-
A short while later with two trackdays under my belt since fitting the supercharger, and after a few data logs the ECU tune seems to be dialled in. The only issue that reared its head was a slipping clutch. So at that point I decided to fit a metallic three puk Exedy clutch, and while at it I figured I might as well take the opportunity to fit a lightweight flywheel. There are a few choices out there but I finally decided on the RCM one, coming in at a very light 3.6Kg, well under half the OEM flywheel weight As I was breaking out the tools, and dropping most of the exhaust system to remove the gearbox I decided to fit a new manifold/header to replace the OEM. I opted to go with an unequal length for the replacement, to help to increase the lower and mid range torque and result in a little more boxer burble, plus it would reduce the increased back pressures from the added boost of the supercharger With the manifold removed it was a good opportunity to fit a new Racer X baffled sump I’d picked up too. Finally got it all fitted and manifold wrapped, as it sits quiet close to the sump I decided to double wrap the manifold, will be no harm for under bonnet temperature anyways. Final bit of work was to change the brake fluid, engine oil, and diff and gearbox oils ahead of the next track-day.
-
So fast forward to the end of 2016 and after a handful of track-days the lack of power was starting to wear thin. With the severe torque dip between 3-4.5K rpm there were a couple of corners on track where this coupled with a long 3rd gear ratio was really highlighting the lack of grunt. I debated with sticking with NA and going the route of a remap and headers but really the smart money goes on forced induction. So a HKS supercharger was chosen, and paired up with an HKS oil cooler. On the advice of Abbey Motorsport who would be mapping the car, I also went with the IAT kit too.
-
I’ve run my racecar on slicks and R888s for the last three years with nothing more than a racerX baffle sump and oil topped up to the max mark on the dip stick. Now saying that I’m not sure I would still recommend it long term, For piece of mind given that my car os only driven on track as I’m in the middle of building my engine I’ve gone with the high flow Remax oil pump, killer B pickup, and an accusump which will be controlled by my AIM dash, alongside the baffled sump I’m hopeful that should address any concerns but I think the Accusump is a wise move at any level.
- 14 replies
-
- oil starvation
- oil pressure
-
(and 2 more)
Tagged with: